首页能源头条推荐资讯详情
锂电池石墨复合电极力-电耦合性能原位测量分析

发布者:
来源:
标签:




DOI:10.19799/j.cnki.2095-4239.2024.1149
本文亮点:1.使用石墨电极来进行原位测量实验设计与分析,开发原位测量手段对复合石墨电极电化学循环过程中的力-电耦合性能进行测试,在小变形模型下,分析了曲率变形与杨氏模量、偏摩尔体积以及应力之间的关系。 2.研究了不同集流体厚度对于复合石墨电极力学性能的影响,提供了一种实时捕捉锂电池电极在电化学反应中的力学响应的原位观测手段,帮助深入理解影响其内部损伤和循环寿命的作用机制。
摘 要 石墨是目前锂电池最常用的负极材料之一,其电化学-力学耦合性能对于锂电池的结构稳定性和循环寿命非常重要。研究通过开发原位测量手段对复合石墨电极电化学循环过程中的力-电耦合性能进行测试,同时开发物理模型,用于分析石墨复合电极曲率、杨氏模量、应变和偏摩尔体积的演化规律,探究对电池寿命性能的影响。研究结果表明,随着锂化过程的进行,石墨电极的弹性模量逐渐增大,表现出硬化趋势,且偏摩尔体积随锂浓度呈阶段性变化。不同厚度的集流体对电极内部的应力、应变有显著影响,较厚的集流体在抑制活性层应变方面效果更显著。同时随着循环次数增加,电极活性层中的应力和应变峰值在第三次循环达到最大,且各循环演变趋势趋于相同。本研究系统性地揭示了石墨负极在电化学反应过程中的力学响应特征及其力学性能的演变规律,为深入理解锂离子电池电极的力学行为提供了参考。
关键词 石墨复合电极;模量;偏摩尔体积;锂离子电池
随着全球范围内对清洁能源及电动汽车需求的日益增长,锂电池产业正在快速地发展与扩张。石墨因其性能稳定、低电压平台和成本低廉而被选择作为商业储能锂电池负极材料。在电化学反应过程中,锂离子的嵌入和脱出,会引起石墨层间距的变化,进而导致石墨颗粒的体积膨胀与收缩。同时由于活性层受到金属集流体的约束,会在电极上产生应力,电极发生弯曲变形,而在电池尺度上表现为电池体积膨胀。此外,在电化学反应过程中,锂离子的嵌入和脱出所产生的扩散诱导应力会使得活性颗粒发生微观结构变化,进而导致电极产生裂纹、分层等损伤,影响锂电池的容量密度和循环寿命。因此,结合原位实验来实时监测复合电极在电化学反应过程中的力学性能,深入探究循环过程中复合电极的力学-电化学耦合性能演化,有利于深入了解商用锂电池的工作机理,进而指导设计出高容量商用锂电池。
原位测量系统可用于准确捕捉锂电池电极在电化学反应中的电化学-力学耦合响应,探究复合材料电极力学性能参数和应力、应变等参量随锂离子浓度的演化规律,深入研究力学响应对于锂电池容量密度和循环寿命的影响机制。目前,已有相关研究开发了原位测量手段并用于探究锂电池电极的电化学-力学耦合机理。其中,利用数字图像相关(DIC)技术研究石墨负极在嵌锂和脱锂过程中的机械演变,发现应变随电极表面形貌的变化而变化。原位拉曼光谱实验被用于分析和讨论变形机制及速率响应特性,量化石墨负极在不同充放电速率下的微观变形。Schweidler等使用原位X射线衍射和原位压力分析技术来监测石墨阳极在充放电过程中的结构变化和体积变化,在阳极/阴极平衡的考虑下,不完全锂化也会导致晶格中产生显著的应变。有研究对多孔石墨电极的锂化和脱锂过程进行了动态观测,讨论了锂离子传输过程中迁移率的演变,以及锂浓度和相变对迁移率的影响。当锂离子嵌入时,石墨颗粒经历一系列的相变过程,形成了层间化合物(LiC)。中子衍射观察石墨电极在循环过程中的相变,揭示了LiC12和LiC6等相的存在及演变。锂离子的扩散性及不同阶段锂化产物的力学性能取决于锂浓度。这种依赖性导致了石墨电极在循环中会发生阶段性的材料特性变化。因此,探索石墨电极在不同锂浓度下、不同循环阶段的循环性能和力学性能的演化过程对提高电极的电化学性能至关重要。
为了研究复合石墨电极在不同锂浓度以及不同循环阶段的循环性能和力学性能的演化过程,本工作采用了曲率原位测试系统对杨氏模量、偏摩尔体积等参量进行定量分析,并且实时监测复合电极在电化学循环过程中的弯曲变形,建立了复合石墨电极在电化学反应过程中的弯曲变形理论模型,用于深入理解复合电极的力学响应机理,并且研究了不同集流体厚度对于复合石墨电极力学性能的影响。结果表明,随着锂化过程的进行,复合石墨电极的应力和模量呈现非线性增加,并且其偏摩尔体积会随着充电状态发生阶段性变化。本研究提供了一种实时捕捉锂电池电极在电化学反应中的力学响应的原位观测手段,帮助深入理解影响其内部损伤和循环寿命的作用机制,能够为储能电池的进一步优化提供力学角度的指导。
1 实验
1.1电极制备
石墨复合电极由质量分数为90%的石墨颗粒、2.5%的导电炭黑和7.5%的CMC混合而成,制备电极浆料时,首先将CMC溶解于去离子水中,然后依次加入石墨颗粒和导电炭黑。搅拌充分后用刮刀将混合均匀的浆料均匀地涂在铜箔上,并在室温下静置6小时,然后转移到真空干燥箱(温度设置为110 ℃)中进一步干燥。为排除活性物质载量不同对电极力-电耦合性能的干扰,在电极制备过程中严格控制涂敷厚度,使所有电极样品厚度一致。此外,在电极制备完成后,均进行了相同工艺参数的滚压处理,确保电极的孔隙率保持一致。这些改进措施确保了变量的可控性,使得研究可以更专注于集流体厚度对力-电耦合性能的影响。集流体和石墨活性层的厚度使用千分尺(mitutoyo micrometer)进行测量,其总厚度为40 µm,而集流体的厚度分别为10 µm、17 µm和22 µm。如图1所示,集流体的应力应变曲线通过动态机械分析系统(DMA Q800)测定,集流体弹性模量由弹性阶段应力与应变比值求解得到,分别为55 GPa、37.5 GPa和36.9 GPa。经过分析,石墨电极孔隙率约为59.62%,活性材料的体积分数约为35.32%。石墨复合电极的初始表面形貌和电极元素能谱(EDS)如图2(a)和2(b)所示。可以看出在电极中C元素的质量分数为97%,这与电极初始材料的比例接近。
图2 石墨复合电极表面形貌和元素能谱图
1.2纽扣电池和模型电池的组装及电化学测试
本工作通过纽扣电池来测试石墨复合电极在循环过程中的容量密度和循环寿命。制备好的电极和锂片(1 mm厚)组装在CR2023型纽扣电池中,石墨电极和锂金属之间使用微孔聚丙烯薄膜(25 μm厚,Celgard 2400)作为隔膜用以防止短路,所有步骤均在手套箱内(O2≤0.1 ppm,H2O≤0.1 ppm,1 ppm=10-6)进行。同时结合模型电池来测量其力-电耦合性能,如图3所示。模型电池设计透明石英窗口用于实时监测电极的弯变形规律。此时,石墨电极尺寸为:长×宽=15 mm×3 mm,锂金属作为对应电极来提供锂离子。其中电解液由1 mol/L LiPF6溶于碳酸乙烯酯和碳酸二乙酯(EC和DEC体积比为1∶1)中制备而成(南京江山能源科技股份有限公司)。
考虑到温度变化对石墨复合电极力-电耦合性能的影响,本研究采用温箱进行温度控制。所有电化学测试均在室温(25 ℃)下,通过温箱保持温度恒定,使用CT-4000-mA NEWARE电池测试系统进行测试,以确保实验环境的稳定性和数据的准确性。对于纽扣电池,充电倍率设定为C/3,充电时间设定为3小时,用以测试复合石墨电极的循环性能和库仑效率。对于模型电池,充电速率设定为C/10,充电时间设定为10小时。此处模型电池选择相对较小的充放电速率以保持锂离子在活性层中的均匀嵌入,有助于减少极化对于复合石墨电极在锂化和脱锂过程中的影响。在电化学循环过程中,用CCD(CM200GE)工业相机实时记录石墨复合电极的变形图像,如图3所示。CCD相机每2分钟拍摄一次图像,同时电池测试系统以1 Hz的频率记录电压、电流、时间和容量等电化学参数。
1.3双层电极弯曲变形物理模型
为了研究不同厚度集流体的复合石墨电极在循环过程中的曲率变化,本工作开发物理模型用于探究其变形与电化学反应直接的关联机理。如图(3)所示,物理模型由集流体和活性层两部分组成,其厚度分别为c和a。定义厚度方向为轴,平面内方向为和轴。在电化学循环过程中,锂离子的嵌入和脱出会导致复合电极活性层的膨胀和收缩,但活性层受到集流体的限制,这种应变不匹配会导致电极弯曲变形。在电化学循环过程中不断捕捉电极的实时变形,结合图像分析软件获得其曲率演化规律,其大小表示为
根据小变形理论,与厚度方向相关的应力和应变分量均为零,方向上的法向应变可写成:
(1)
式中,
是=0平面上的面内应变,
是曲率。为便于分析,本研究假设活性层是宏观各向同性和完全弹性的。因此,活性层和集流体的本构关系可表示为:
(2)
通常情况下,石墨电极的杨氏模量是锂离子浓度的函数。然而,由于实验选取的充放电倍率相对较低,因此可以忽略其厚度方向上的浓度梯度。其中,1代表电极活性层的杨氏模量,c代表电极铜箔的杨氏模量。
代表摩尔体积变化。
分别代表集流体和活性层的应力。电极的边界约束:
(3)
(4)
式(2)、(3)联立求解:
(5)
联立公式(2)、(4)、(5),可得一个二元一次方程:
(6)
其中,
分别为铜箔的厚度比、模量比,两个电极测试的曲率可以用
=, )来表示。因此可以推导出关于电极曲率,厚度比以及模量的方程:
(7)
通过设计两种不同厚度的比电极,联立求解出模量:
(8)
为简化计算,其中:
由公式(8)得到模量结果,从而进一步求解得循环过程中偏摩尔体积的变化:
(9)
2 结果与讨论
为了分析复合石墨电极的电化学性能,对不同集流体厚度(分别为10 µm、17 µm和22 μm)的纽扣电池进行测试,以获得其循环性能,如图4(b)所示。在初始循环过程中,固体电解质界面(SEI)的形成导致部分锂离子被消耗,从而使纽扣电池的比容量相对较低。此外,石墨电极的表面缺陷、不可逆嵌锂现象以及电解质分解等因素同样会引起锂离子的损耗,进一步降低初始库仑效率。在前70个循环,石墨电极比容量基本保持不变,其中22 µm电极的比容量明显低于其他样品。在120次循环后,集流体厚度10 µm、17 µm和22 µm的电极其纽扣循环比容量分别为369.98 mAh/g、357.5 mAh/g和337.46 mAh/g。经长时间充放电循环后,10 µm集流体的复合石墨电极在电化学方面表现出较好的性能,保持着较高的容量。为了更好地分析电极力学性能的表现,本研究还采用了原位测试系统对不同电极进行力电耦合性能测试。
图4 (a) 电极弯曲变形和 (b) 循环寿命图
在嵌锂过程中,锂离子进入活性层,导致石墨颗粒发生膨胀,集流体对活性层的膨胀施加限制,这种限制作用会引发电极的弯曲变形。复合石墨电极的曲率与电压随时间变化趋势如图5所示。随着每次充放电周期的进行,电极的活性颗粒经历膨胀和收缩,由于集流体的约束,这种膨胀和收缩会引起周期性的弯曲变形,导致曲率在每个循环中出现周期性的增大与减小。如图5(a)所示,嵌锂过程中的弯曲变形逐渐增大,而脱锂过程中则出现弯曲变形的减小。随着循环次数的增加,曲率逐步增大。实验结果表明,随着循环次数和锂浓度的增加,曲率呈现逐渐增大的趋势,且在厚度为10 µm的电极中,锂化过程中的弯曲变形更为显著。因此,集流体的厚度越薄,集流体与活性层之间的不匹配越严重,从而导致弯曲曲率的增加。如图5(b)所示,两个电极的电压曲线呈现相似的趋势,表明尽管使用不同厚度的集流体,电极的反应行为几乎相同。
图5 (a) 石墨复合电极五循环曲率和 (b) 电压变化曲线图
由于在初始循环中的SEI形成具有更复杂的反应机理,为了避免其对电极机械响应的影响,本研究选择第三循环的变形过程进行。如图6所示,薄集流体的电极曲率增加速率更快。结果表明,由于集流体的厚度不同,它们的曲率演变趋势也不同。随着充电状态的推进,三个电极的曲率逐渐增大。集流体厚度为10 μm的电极曲率在SOC100%时达到峰值,为312 m-1。集流体厚度为17 μm的电极曲率峰值为220 m-1,而厚度为22 μm的电极对应的曲率峰值为165 m-1。基于第三次循环过程中的曲率数据,进一步分析石墨复合电极力学性能演变。
经过对第三循环的曲率数据进行处理,将其代入公式(8),计算得出第三循环中电极模量的变化,如图7(a)所示。为消除活性层对电极力学性能的影响,使用刮刀将涂覆在集流体上的电极浆料分布均匀,使得各样品活性层厚度保持在40 µm,经计算其面密度均为1.097 mAh/mm²左右。如图7(a)所示,三种样品的活性层模量变化一致。在充电过程中,锂离子的嵌入导致石墨材料膨胀,进而改变其力学性能,并增加石墨层内作用力。结果表明,活性层的杨氏模量随着锂化程度的增加而逐渐增大,充电过程中模量增大,放电过程中模量减小,且活性层随锂化进程逐渐硬化,该趋势与已有研究结果一致。
图 7 石墨复合电极第三循环中的 (a) 杨氏模量和 (b) 偏摩尔体积曲线图
在锂化过程中,复合电极的弹性模量随嵌锂时间逐渐增大。随着锂化程度的增加,石墨的层间距会发生膨胀,形成LiC化合物,因此石墨复合电极逐渐表现出硬化趋势。同时,偏摩尔体积的变化可通过公式(9)计算得到。如图7(b)所示,在锂化过程中,活性层的偏摩尔体积在达到30%SOC之前几乎与容量呈线性增长,石墨电极的膨胀行为较为均匀,嵌锂未达到饱和。然而,在30%~68%SOC区间,活性层的偏摩尔体积呈现出平台区域,这一平台区域可能对应于特定阶段产物的形成(如LiC12),而在68%~100%SOC范围内,偏摩尔体积再次转变为线性增长,更多的锂离子嵌入使体积迅速增大,且此时石墨已近饱和相(如LiC6),这也会加剧电极的硬化趋势。
如图7(b)所示偏摩尔体积展现出随着嵌锂时间的增加先增加后渐缓保持,并在后期逐步增长。并且基于图5(a)多循环曲率数据可以发现,电极在单个循环结束后并不会回到初始状态,有一定的残余变形,并且随着循环数增大,残余变形会逐渐积累增加,而这也可能是活性材料中锂离子的插入和脱出引起的循环体积膨胀和收缩;另一种可能是与石墨中SEI的形成和锂离子残留以及不可逆的微观结构变化和损伤有关。
本研究进一步分析了三种不同厚度样品的力学性能差异,主要针对电极的面内应变和应力进行了详细展开。为消除第一循环中SEI层生成对结果的影响,提取了后四个循环的数据,对不同厚度集流体电极的多循环阶段变化进行了应力应变分析。同时,为去除各循环积累残余应变的影响,对每个循环的曲率数据进行了归一化处理。将处理后的曲率数据代入公式(5),得到了活性层的应变曲线。图8展示了集流体厚度分别为10 µm、17 µm和22 µm的电极样品中,活性层的应变和应力随时间变化的情况。
图8 不同厚度集流体石墨复合电极活性层表面处 (a) 应变;(b) 应力图
在锂化过程中,石墨复合电极体积逐渐膨胀,活性层受集流体的约束作用,内部产生应力,并随锂离子浓度的增加而增强。如图8(a)所示,单个样品中,复合电极的平面应变随着锂离子的嵌入而增大,在脱锂过程中则减小,此现象符合应力演化规律。在多循环过程中,应变变化趋势保持一致且基本平行。在第三循环后,随着锂嵌入,所有循环的最大应变保持在较稳定的水平。与其他两种电极相比,较薄集流体(10 µm)样品的应变增长相对较快,且应变峰值最高;而22 µm样品的应变最小,这表明更厚的集流体对活性层的限制作用更强。在电极活性层表面,单循环过程中,随着锂离子的嵌入,活性层内应力增加,锂离子脱出时应力随之减小。每个循环的应力变化趋势基本一致,与17 µm和22 µm样品相比,10 µm集流体样品的活性层受到的应力更大。研究结果表明,在前三个循环中,三个样品的应力应变峰值均随循环次数增加而逐步提升,并在第三循环达到稳定。之后的脱锂与嵌锂过程中,应力应变变化趋于相同的规律。
3 结论
本研究聚焦于室温25 ℃锂电池中复合石墨电极的电化学-机械耦合特性,旨在通过弯曲变形分析深入探讨石墨复合电极的工作机制。采用原位曲率测试技术采集曲率变化数据,通过纽扣电池的充放电循环获取循环性能,用以系统分析石墨复合电极在电化学和机械响应方面的特性。研究过程中改进了原位实验技术及相关理论模型,结果显示,在锂化过程中石墨电极的弹性模量逐步增加,偏摩尔体积则呈现阶段性变化。此外,针对不同厚度集流体的内部应力、应变变化,研究发现随着循环次数的增加,电极活性层所受的应力、应变峰值逐步提升并在第三循环达到最大,且多周期循环中的应力、应变变化趋势基本一致且呈平行分布。较厚的集流体在抑制活性层应变方面表现出更优的效果。本研究进一步揭示了石墨负极在不同循环次数及锂浓度条件下脱嵌锂过程中的力学性能变化规律。所采用的原位曲率测试方法为复合石墨电极的深入分析与机理研究提供了重要的参考。未来的研究将进一步探索石墨复合电极在高温和低温条件下的力-电耦合行为,以揭示温度变化对其性能的影响,从而为适应实际应用中的复杂环境提供更全面的指导。
反馈举报

声明:以上信息仅代表发布者自身观点,并不代表本平台赞同其观点,也不代表本平台对其真实性负责。
大家都在看
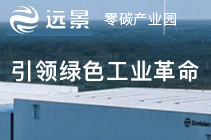
广告
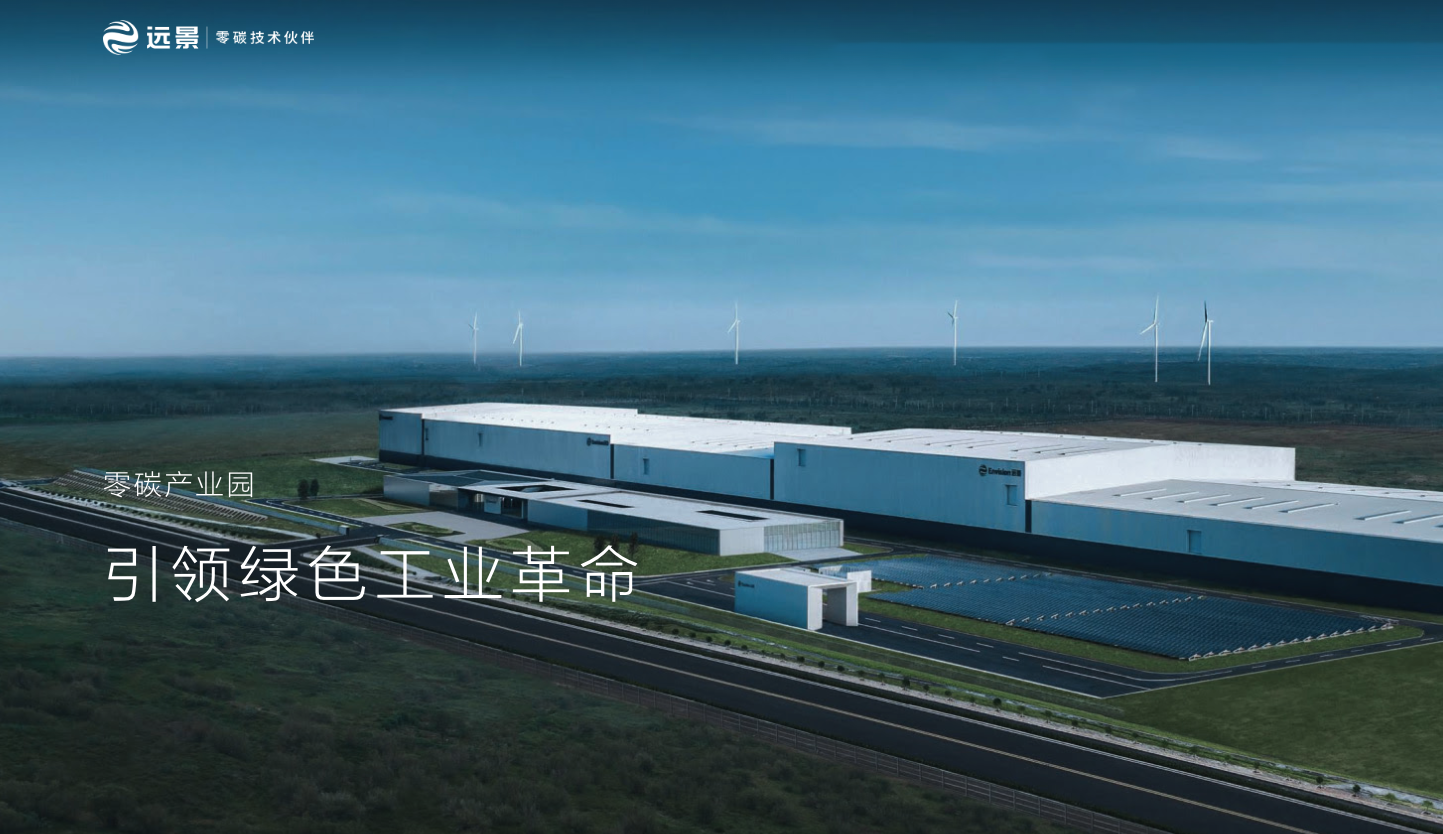
广告
评论 0
网友评论仅供其表达个人看法,并不表明平台立场。全部评论
加载失败
总发布:7178粉丝:17
相关推荐
- 加载失败
能源资讯
- 加载失败
能源资讯
- 加载失败
- 加载失败
- 加载失败
- 加载失败
- 加载失败
- 加载失败
- 加载失败
- 加载失败